Electrochemical deposition (ECD):
Copper is used as interconnect material in the ICs. Copper can be deposited by PVD or CVD. However, the copper deposited by ECD has a lower resistivity and a better fill characteristic. The basic principle of electrochemical deposition is very simple. One can even try it at home. You can take two normal batteries and stack one on top of another and get a 3 volt battery combination. Two metal plates (e.g. key or shaving blade) should be connected to the positive and negative end by wires. In a glass beaker, some water and copper sulfate should be taken. If the metal plates are dipped inside the solution, without touching each other and then the connected to the batteries, then copper will deposit onto the metal connected to the negative terminal and oxygen will evolve from the metal connected to the positive terminal. In this system, the metal connected to the negative terminal is called cathode and the metal connected to the positive terminal is called anode. Using the same principle, gold or silver is also coated on inexpensive ornaments.
We have to remember that silicon is a semiconductor and the wafer must be made conductive for electrochemical deposition. Therefore, a thin layer of copper is deposited on the wafer using PVD or CVD first. This is called seed layer. Then the wafer is kept in a tank containing copper sulfate solution. The negative terminal of a voltage controlling system is connected to the wafer while the positive terminal will be connected to a copper block. When copper is deposited on the wafer, the copper content of the solution will decrease. If we use copper block as anode, then copper will dissolve from it and the solution will have a uniform and constant copper content. By controlling the temperature of the bath and the voltage applied, the thickness of the copper deposited can be controlled.
Apart from copper sulfate, a few other chemicals are usually added to the bath. This enables the deposited film to have good quality, without voids. Fig 3.20 shows a poor quality deposit and the good quality deposit. Certain large organic chemicals, called macromolecules, are added to the bath to obtain a leveled surface. These molecules tend to adsorb on the surface and suppress the deposition rates. They are more likely to adsorb on the flat surface and less likely to adsorb inside trenches and holes. Thus, they reduce the deposition rate on the top surface, but do not affect the deposition rate inside the trench and holes significantly. These are called suppressors or levelers. Certain chemicals called accelerators are also added to the electrochemical bath. They improve the deposition rate. They compete with suppressors in adsorbing to the surface and tend to adsorb more inside the trenches and holes. They also lead to less surface roughness and more uniform grain size of the deposit. They are sometimes called as brighteners. The addition of suppressor and brighteners in appropriate concentration makes the ‘bottom up’ fill possible in electrochemical deposition of copper. Note that the mechanism of action of suppressors and brighteners are not always supported by experimental evidence and in many cases remain as hypothesis. However since they result in good quality film, they are used commercially.
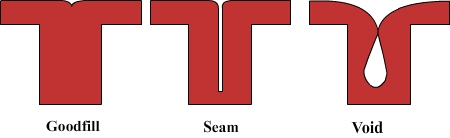
FIGURE 3.20. Examples of poor quality deposits and good quality deposits
While PVD or CVD can be used to coat copper on the wafer, it is used only for coating the seed layer. This is because superior quality copper is obtained by electrochemical deposition. For example, the electrical resistance of the copper obtained by electrochemical deposition is lower than that obtained by CVD or PVD. Another important property called electromigration-resistance, is more for electrochemically deposited copper. Electromigration is the tendency of the material to move with flow of current. If electromigration is high, then the wire will degrade soon and hence is not suitable. If electromigration resistance is high, then the material is considered as suitable. Thus, the ideal interconnect material should have low electrical resistance and high electromigration resistance. If the grain size of the deposited metal is large, it will tend to have better electromigration resistance. Since electrochemically deposited copper has large grain size and achieves low electrical resistance and high electromigration resistance, this method is used in semiconductor industry for depositing copper.
|